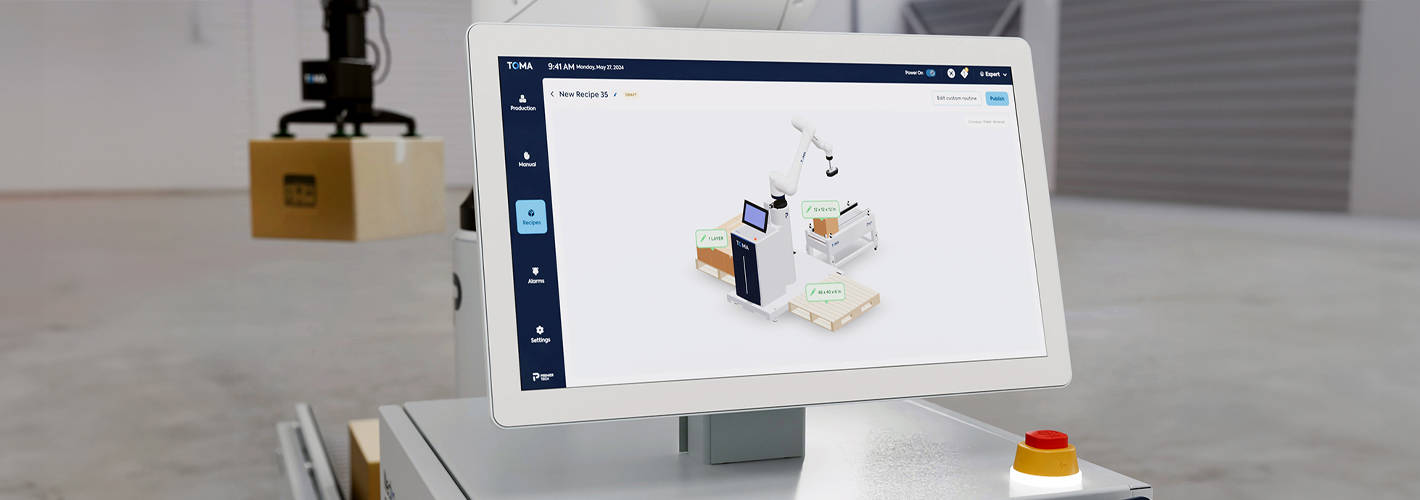
Integrating cobots into end-of-line packaging made easy
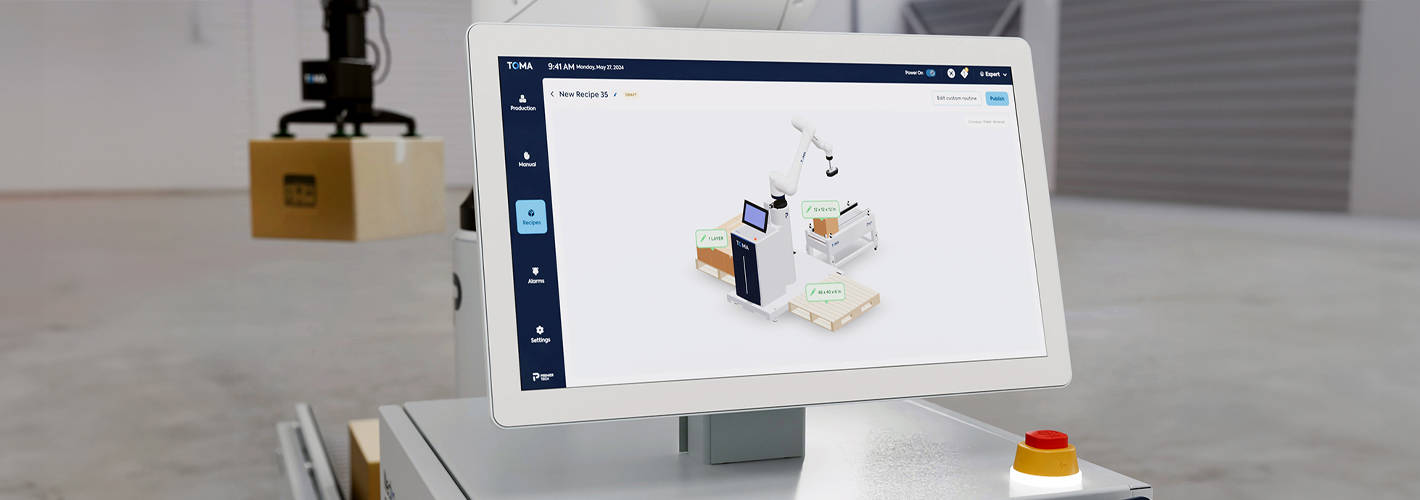
Collaborative robots, or cobots, are making a big impact in end-of-line packaging systems. Unlike traditional robots, cobots are designed to work seamlessly alongside humans in shared workspaces: they tackle repetitive tasks with precision, speed things up, and often save you money. However, despite their promising advantages, cobot integration isn’t always a piece of cake. Let’s take a deeper dive in this short article.
It is no secret that cobots are catching the eye of many business owners, with their many appealing features. Efficient, safe, and moveable, cobots are set to double in use over the next five years. As they take center stage they are clearly redefining modern automated packaging lines.
However, despite their apparent appeal, when it comes to programming a cobot for a unique operating line, questions emerge almost immediately: How easy is it to program? Do I have to know a coding language? Will I have to hire a specialist? Let’s start by laying out the benefits of collaborative robots.
First things first. Why get a cobot?
Designed with limitations that allow them to work safely alongside humans, cobots can be an asset for your business, small or large, for many reasons.
Integrating a cobot can help you:
- Enhance efficiency by handling repetitive tasks such as picking, packing, and sorting far faster than human workers.
- Decrease the risk of injury, meaning less downtime and healthcare costs and significant savings over time.
- Improve precision and quality of end-of-line packaging by picking and stacking with high accuracy.
- Boost job satisfaction by letting human workers focus on value-added tasks that are both rewarding and less hard on the body.
- Save space and money as they generally take up a smaller footprint and cost less than an industrial robot.
- Tackle multiple jobs as cobots are usually mobile and can be repositioned in your plant according to your needs.
With a lineup this impressive, it is only natural that cobot integration is becoming a serious consideration for many business owners. However, one of the biggest hurdles is the complexity of cobot programming and set-up. In other words, how do I get started with cobots in the first place?
Cobot integration: how it works
Integrating a cobot into an end-of-line packaging system usually involves a laundry list of steps including: determining what cobot best suits your needs, making the purchase, finding all the hardware, doing the software setup, configuring the equipment, testing the equipment, doing a risk assessment, troubleshooting, and training... and that’s just a summary.
Programming a cobot for the specific tasks it will perform is just one part of this process—but it can feel like one of the most daunting. You will need to consider the cobot’s movement paths, speeds, and interactions with other equipment—all while keeping safety as a key priority.
In this step, you typically face a number of questions such as:
- How do I program the cobot to handle my specific product?
- Where does the cobot need to be placed on my operating floor?
- When palletizing, where do I need to place my pallet in relation to the cobot?
Overall, even this one step of the cobot integration process is complex. Now, you might be wondering: why would I want a cobot if it is so hard to deploy? Enter the appeal of cobot solutions that prioritize a low-programming approach.
Easy programming cobot solutions
Many companies have recognized that businesses do not have the capacity to invest significant time or money for the set-up stage when it comes to cobot integration.
These innovative solutions emphasize ease of use, intuitive interfaces, and simplified programming to make automation accessible to users without extensive technical backgrounds.
Benefits of low-programming cobot solutions
User-friendliness
When a solution does not need programming skills, anyone can use the equipment, no matter their technical background. This lets more team members get involved and boosts overall productivity.
Efficiency boost
No-code solutions mean quicker deployment and a faster ROI for a couple of reasons. With a simple HMI and no need for complex programming, the set-up process is quick and the cobot can begin performing quickly. Further, easy-to-use systems that need little or no programming mean less training and support. This shortens the payback period while improving performance.
Error reduction
Finally, a straightforward integration process reduces the chances of operational issues, leading to a smoother, more efficient workflow.
Your gateway to automation
Cobots are increasingly attractive in the world of end-of-line packaging thanks to their efficiency, safety, and flexibility. While programming concerns may arise, such as ease of use, need for coding knowledge, or hiring specialists, there are solutions that eliminate these hassles. The right cobot can serve as an easy entry point into the world of modern automation.
If you are curious about the power of no-code cobot solutions, you are in the right place. With key industry knowledge and 35 years of experience in end-of-line packaging, Premier Tech has developed a new offering with the easiest programming on the market: creating the TOMA™ difference. TOMA™ is an innovative solution for cobot integration that anyone can use, no technical know-how required.
Looking for something simple and code-free?
TOMA™ is all about making automation friendustrial™, and our team has made the power of cobots accessible in an all-new way. Learn more about our products.