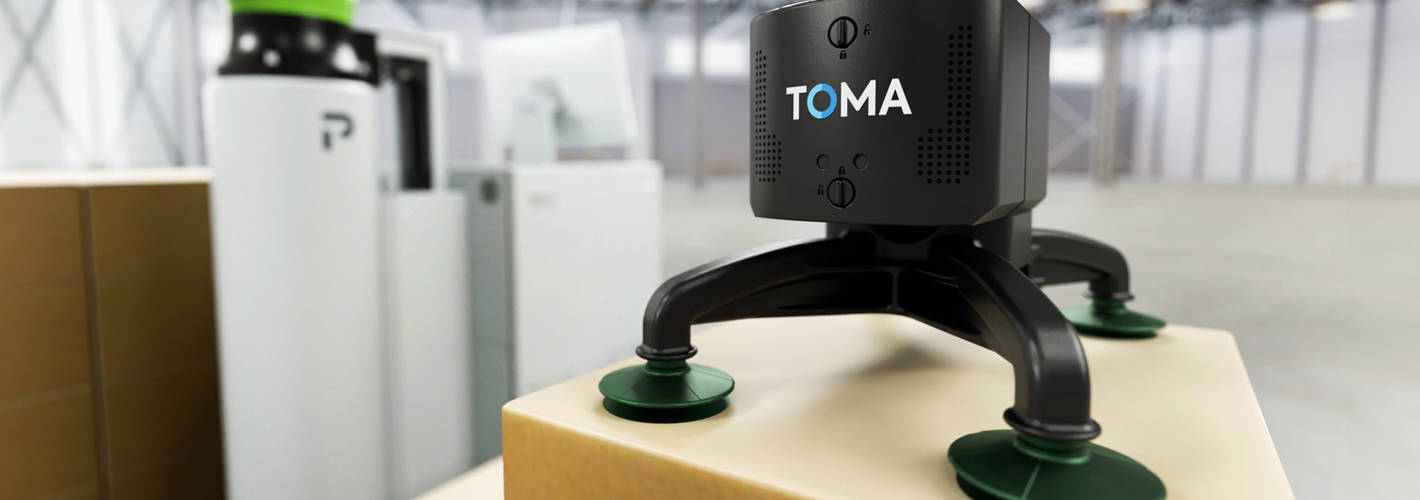
5 reasons why a cobot palletizer might be your team’s best new ally
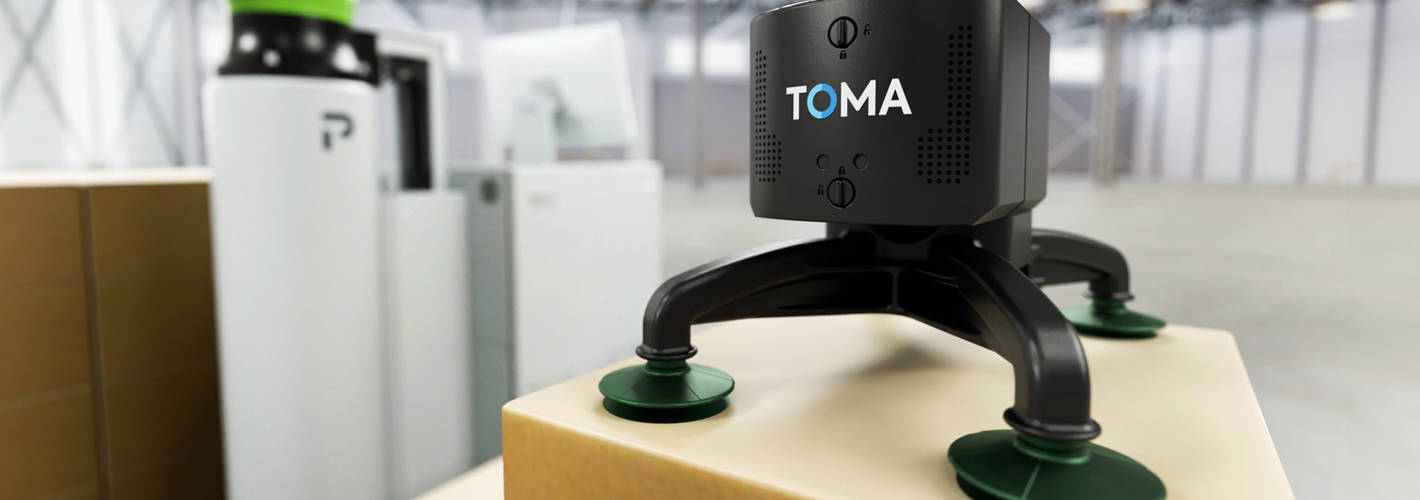
If your business involves shipping or storing products, you are likely familiar with the repetitive tasks of palletizing—stack, secure, inspect, and repeat—and the challenge palletizing can be for your workforce. In this post, we will explore five compelling reasons why a cobot palletizer might be the best investment for your end-of-line packaging operations.
Ever find yourself wishing there was an easier way to stack products on a pallet? Well, here is a little secret that might just be the breakthrough you need: collaborative palletizing robots, or cobots. These technological marvels are quickly becoming a hot topic for workplaces both large and small. When it comes to palletizing applications, they’re a no-brainer.
Whether you are a health and safety manager aiming to enhance workplace ergonomics or a business owner looking to automate palletizing for the first time, cobots offer exciting possibilities.
5 advantages of investing in a cobot palletizer
Safe, lightweight, and a less costly alternative to an industrial robot, cobots could be the perfect solution for you. Here are five reasons why investing in a cobot palletizer might be the best next hire for your end-of-line packaging operations.
1. Improved safety
Because they never tire, cobots reduce the risk of workplace injuries related to manual handling and repetitive tasks. For a small business, collaborative robot palletizing can mean a safer work environment, in turn improving worker satisfaction and reducing turnover. For a large business, cobots can mean fewer workplace accidents and lower insurance costs.
2. Efficiency boost
Thanks to a combination of advanced sensors and smart design, collaborative robot palletizers work quickly and accurately. This reduces the time and effort involved in manual palletizing. For a small business with limited staff, this can translate immediately into increased throughput and reduced labor costs. For a large business, palletizing with a collaborative robot can streamline high volume processes and maintain consistent production levels.
3. Greater flexibility
Cobots can be easily programmed for different palletizing patterns. Whether you are a small business owner or managing a large enterprise, you can use this flexibility to your advantage by handling seasonal variations or new product lines without a major equipment switch.
4. Cost savings
While the initial cost of a cobot might seem high, they are actually much less expensive than their traditional industrial robot counterparts. The long-term savings are well worth considering. Typically, cobots pay for themselves within months through reduced labor costs, increased efficiency and lower operating expenses.
As an added plus, cobots tend to have fewer moving parts and are typically designed to allow easy access to components for tasks like cleaning and inspection.
5. An empowered workforce
Cobots are poised to transform the experience of work by making automation more straightforward than ever before. Often, workers do not need specialized programming skills to set up and operate cobots. Instead, they can develop recipes and palletizing patterns through an intuitive interface. Employees can quickly set up the cobots to handle repetitive or physically demanding tasks while they are freed up to focus on more complex or strategic jobs.
Palletize with cobot power
In sum, the right cobot brings safety, efficiency, flexibility, cost savings, and scalability to the table in a single package. Opting for a cobot in your palletizing operations is a forward-thinking choice that will benefit your workforce for years to come.
Ready to invest in your future?
Transform your end-of-line packaging with the TOMA™ palletizer, featuring a cobot arm powered by FANUC and an exceptionally user-friendly interface. Visit our palletizer page to learn more.