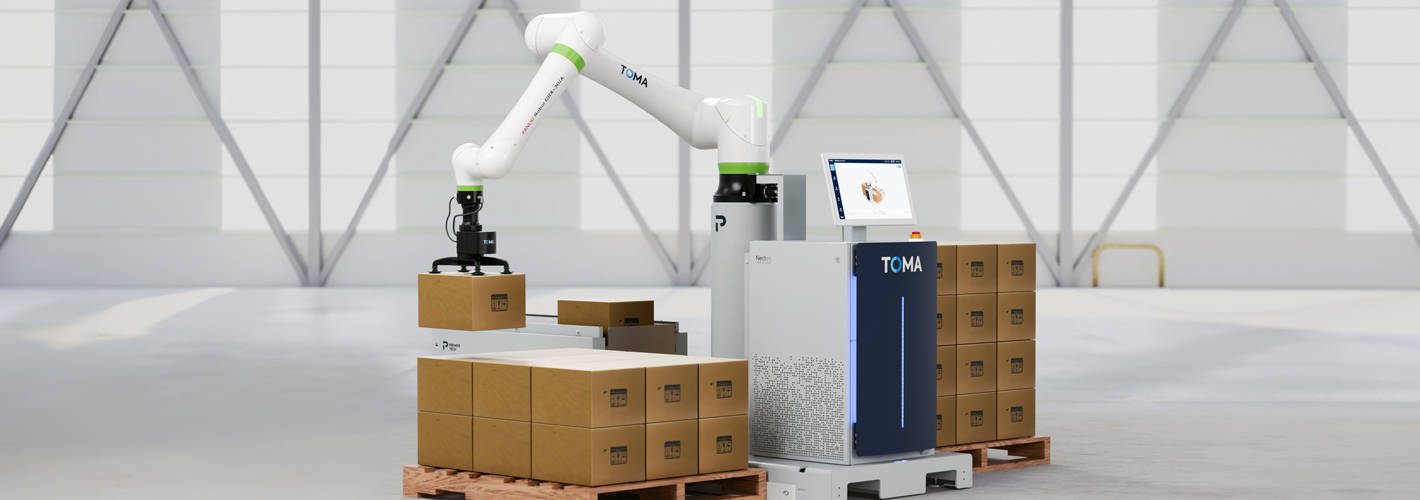
What are the differences between a robot and a cobot: a beginner’s guide
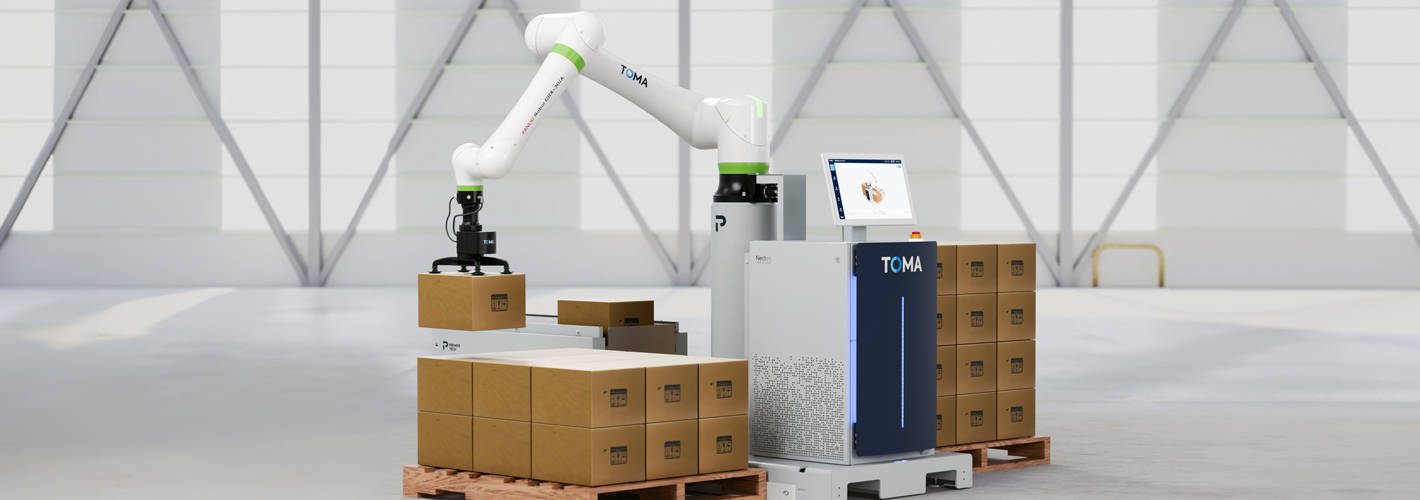
Looking into the world of automation? You may have encountered the terms “robot” and “cobot.” Though the distinction between them might seem as simple as a single letter change, the impact on the manufacturing floor is anything but minor. In this blog post, we’ll break down the differences between robots and cobots.
If you’re exploring your options for automating your packaging line, getting a clear picture of the difference between a robot and a cobot is essential. By recognizing key advantages and drawbacks, you’ll be able to understand the unique benefits of each technology and make the best choice for your operating floor.
Let’s examine the differences together, starting with some quick definitions.
Quick definitions
Industrial robot
Industrial robots are used across various sectors such as automative manufacturing, the food and beverage industry, and pharmaceutical and medical device manufacturing. Powerful and robust, industrial robots are heavy lifters who can take over functions like welding, assembly and material handling, such as palletizing. Typically, industrial robots operate within enclosed, defined workspaces.
Collaborative robot
Collaborative robots, or cobots, are also well-suited for various sectors. However, they are better thought of as co-workers in the world of automation. Unlike traditional industrial robots that must operate in isolation behind safety fences, industrial collaborative robots are equipped with advanced sensors and safety features so that they can work side by side with humans. Their primary goal is to take over repetitive or demanding tasks, creating a more dynamic environment for human workers.
Now, let’s take a closer look at some of these key differences.
Differences between robots and cobots
Safety
Collaborative robots are made to work alongside people without the need for external safety devices (in accordance with risk assessment). Because of this, operators can enjoy more versatility, benefit from flexible mounting options such as on trolleys or pedestals and save significant production space. Additionally, some cobots, like the FANUC CRX-30iA cobot, have force sense modules to prevent collision and protect humans working in close proximity.
In contrast, because of their speed, power, and size, industrial robots require safety measures like enclosures to reduce risk. Of course, robots do have safety features, but they are primarily designed for efficiency and a high-speed production environment. Simply put, industrial robots are far too heavy and fast to allow humans to be too close.
Applications and speed
Industrial robots are in their element when it comes to high-speed, high-volume tasks. They are frequently used to pack and palletize heavy-duty products but can also handle small, lightweight items with ease. Industrial robots can be adapted for various speeds and levels of automation.
Cobots are ideal for more flexible and lightweight end-of-line packaging applications (though cobot technology is in constant evolution and achieving higher and higher payloads). Currently, the heaviest payload a cobot can handle is 25 kg. In settings like smaller-scale consumer goods packaging, cobots can work alongside human operators to handle tasks like picking and placing with precision. With safety in mind, they generally work at a reduced pace.
Cost considerations
Generally, collaborative robot prices are more affordable than their traditional robotic counterparts. Notably, they do not require the extensive safety structures necessary for a robot, which contributes to their cost-effectiveness. Plus, the cost to maintain collaborative robots is generally simpler and infrequent and employee training time is minimal. Over time, the total cost of ownership (TCO) for a cobot is generally lower.
In the case of traditional robots, you have to consider the added cost of safety infrastructure, other elements like conveyors, scanners, or checkweighers and specialized programming expertise. Industrial robots have greater cycles than cobots, meaning more frequent grease changes, among other ongoing maintenance costs. All that said, traditional industrial robots do tend to provide a higher return on investment (ROI) when you consider their increased performance and productivity.
Flexibility
Cobots are highly moveable and adaptable, making them an asset within working environments with evolving needs. Because they do not necessarily need to be anchored to the floor, they can be shifted around the plant to the places they are most needed. As compared to their robotic counterparts, cobots also often feature user-friendly programming interfaces. The ease of programming means cobots can be quickly reconfigured for new tasks without the need for extensive coding knowledge.
Where cobots are quite fluid in their application, industrial robots are rigid. They are typically made to handle specific, repetitive tasks and are usually bolted to the floor upon installation. Once they are set up, industrial robots are not easily moved or repurposed, making them less suitable for environments where flexibility is key.
Making the decision
How do you know whether a robot or a cobot is best for your application? Here is a summary of the differences between cobots and traditional industrial robots:
Cobots | Industrial robots | |
---|---|---|
Safety | Require less physical safety features due to lower speed and integrated safety features | Require safety barriers due to speed and power, and no integrated safety features |
Applications and speed | Less picks per minute and preferred for lighter products | Can handle a higher pick rate per minute, versatile for light or heavy items |
Cost considerations | Lower upfront cost, faster ROI | Higher upfront cost, higher ROI for high-speed applications. Additional costs to consider for safety measures and maintenance |
Flexibility | Highly adaptable and moveable in a production line, easy to program | Usually need to be secured to one spot and given a single job to do |
The choice is yours
We hope you now feel confident in understanding some of the basic differences between robots and cobots. By keeping in mind aspects like safety, applications and speed, cost considerations or flexibility, you can make a well-informed decision that fits your business requirements when it comes to automation.
Ready to get started right away? If industrial robots seem like a better fit, Premier Tech has a complete range of robotic palletizers for you to discover.
Do cobots seem like a better choice? Now, with key industry knowledge and decades of experience in end-of-line packaging, Premier Tech has developed a brand-new offering with the power of cobots. Check out the TOMA™ palletizer, a plug and play solution that makes cobot integration easier than ever.
Interested in the power of cobots?
Premier Tech’s latest offering, TOMA™, is all about making automation friendustrial™. Head over to our TOMA™ Palletizer page to learn more.